Q. What is English Netting, and how is it different from nylon net or tulle?
A. English netting is a very soft, pliable and drapeable fabric used for bridal veils, bridal gown overlays and as a basis for machine embroidered lace. It’s most often 100% cotton or a blend of cotton/polyester. The threads are matte finish and slightly thicker than most other nettings. It’s characterized by hexagon shaped holes. The netting is sometimes used for trim on knit garments due to its slight stretch. English netting gives the look and drape of silk without the added cost.
Nylon net is much stiffer and has larger holes than either tulle or English netting. It’s available in wide widths (up to 108”) and is used to add fullness, like on a costume or tutu. Because of its crispness, nylon net isn’t very comfortable for a garment as it’s too stiff.
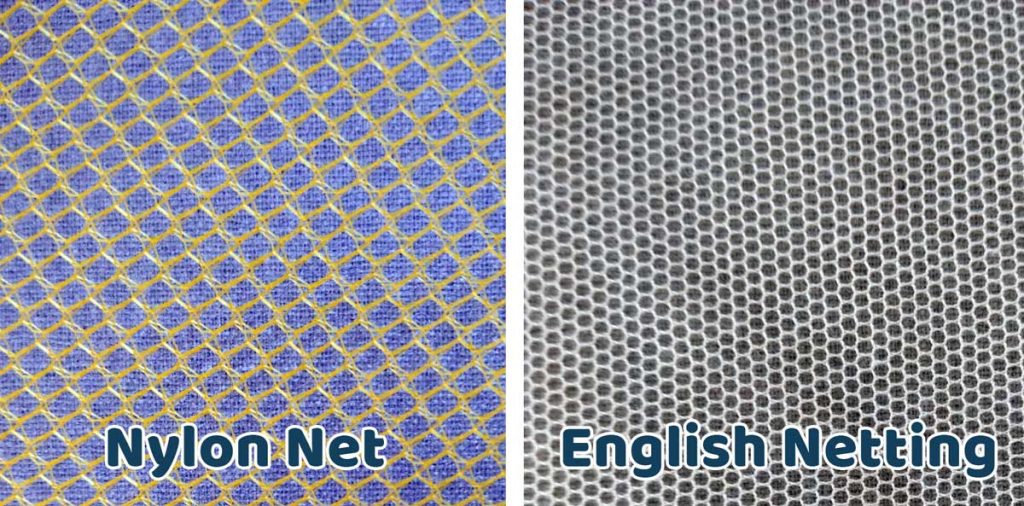
Tulle is a finer version of nylon net with smaller holes and a softer touch. Tulle is sheerer than either of the other two nettings mentioned so it’s often used most often for bridal veils.
Q. Why are some fabrics made from more than one fiber?
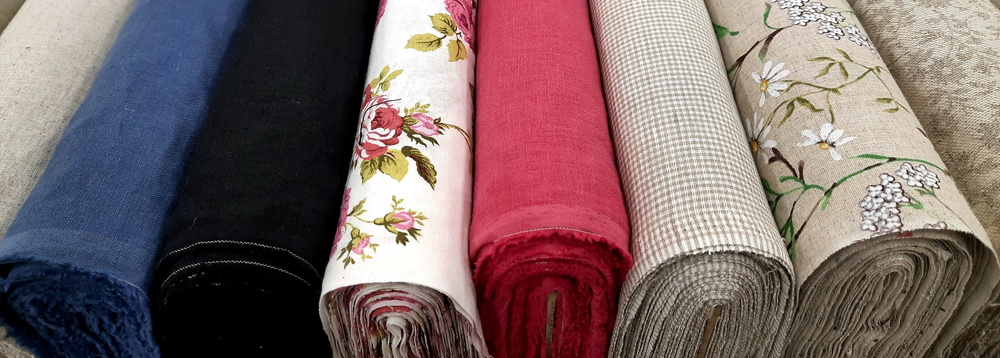
A. Fibers are often blended to take advantage of the attributes of each. For example, some fabrics have a small amount of Lycra added for stretch, or a bit of silk is sometimes added to cotton or wool for added sheen. Polyester is often blended with cotton to improve wrinkle resistance. Fibers are also blended to help with cost—luxury fibers like cashmere or alpaca can be added to wool in small amounts to create a better hand at a still reasonable price. When caring for blended fabrics, be sure to follow the bolt instructions for proper laundering/cleaning methods, and be aware of the blended fibers in choosing an iron temperature for pressing.
Q. Do I need to pre-shrink fabric before cutting out a garment?
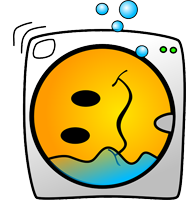
A. The answer depends on the fiber content of the fabric. Look for guidance on the bolt end, but as a general rule, you should pre-treat the fabric as it will be cared for in the finished project. If the fabric is washable, send it through a wash/dry cycle before cutting. If you’re concerned about shrinking, multiple launderings may be in order. Fabrics like denim and flannel will often shrink more with each repeated washing, so it’s a good idea to purchase a little extra fabric to compensate for that. Note that fabric shrinkage amounts are often listed on the bolt end with indicators like “3-4% residual shrinkage may occur”. That amount of shrinkage can affect the fit of a garment.
For dry-clean-only fabrics, either take them to the drycleaner to be steam shrunk, or complete that process at home. If you’re working with home décor fabrics, steam-press them, but do not launder as protective finishes may be removed.
Q. I bought fabric for a jacket but after washing it, it’s way too soft to hold its shape. Is there anything I can do to salvage it?
A. The easiest way to change the fabric hand and make it firmer for your project is to fuse interfacing to the wrong side. A lightweight tricot knit interfacing can be fused to all the cut pieces to add body and support to make it more appropriate for the intended project. Some prefer to fuse the interfacing to the yardage prior to cutting instead of trying to match it up to individual cut pieces later. You’ll need a large flat surface and plenty of steam, and perhaps a press cloth, depending on the interfacing brand and application instructions. Be sure to follow the instructions for applying it and allow the fabric to cool flat before moving.
~Linda Griepentrog is the owner of G Wiz Creative Services and she does writing, editing and designing for companies in the sewing, crafting and quilting industries. In addition, she escorts fabric shopping tours to Hong Kong. She lives at the Oregon Coast with her husband Keith, and three dogs, Yohnuh, Abby, and Lizzie. Contact her at .