Batik is a wax-resist dyeing technique that uses wax and dye to create stunning designs on fabric that are both artistic and symbolic. The process is similar to silk painting. The word “batik” comes from the Javanese words amba which means wide, and titik which means create dots to form lines.
The art of batik dates back over two thousand years, with evidence of its practice found in the Far East, Middle East, Central Asia, and India. However, it flourished in Indonesia, particularly on the island of Java, where artisans developed highly intricate designs with deep cultural significance. Traditional Javanese batik often features motifs representing nature, spirituality, and social status. The method spread globally through trade and colonization, influencing textile traditions worldwide.
Batik is recognized by UNESCO as an Intangible Cultural Heritage of Humanity and remains an important cultural craft in Indonesia and other parts of the world, with both hand-drawn (batik tulis) and stamped (batik cap) techniques still in use. Today, batik is widely used in quilting, garment-making, and home decor projects. However, working with batik fabric requires special considerations due to its unique manufacturing process.
A Fabric to Love
Most modern batiks are usually printed on cotton and silk but can also be found on rayons. The modern method uses a large block with an intricate wire pattern that is dipped in wax and then stamped on the cloth before dying. Most of what we currently see on the market also feature a wide array of colors, although the traditional blues, browns, and oranges are big sellers.
- One-of-a-kind designs – No two projects made from batiks will ever look alike because of its unique creation process, so exclusivity is assured.
- Global influence –Batiks feature an ethnic flair with a strong following in the fashion world.
- Timeless appeal – Batik prints are not dated by season and are suitable for year-round wear.
- Versatile applications – Batiks remind many of the tropics, which makes them a popular style for wrap skirts, sundresses, and beach cover-ups, as well as pillows, throws, and summery home-decor accents.
- Quilting magic – Quilters love batiks because their colors naturally blend with many other styles. Unusual effects can be created by cutting them randomly, and they add unique textures without having to use traditional florals or solids.
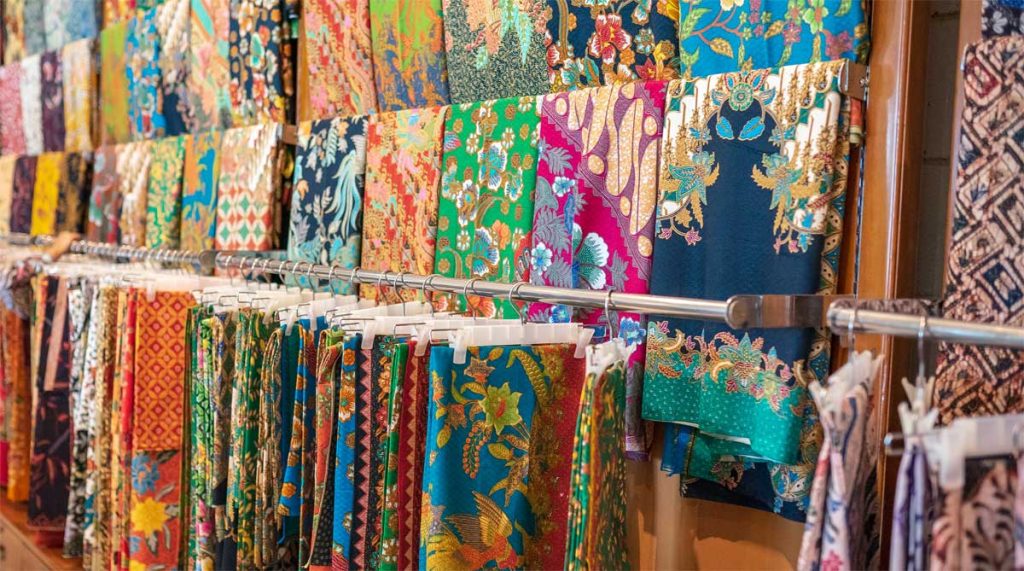
Whether used in fashion, quilting, or home decor, batiks continue to enchant with their artistry, heritage, and endless creative possibilities.
Sewing Tips for Batik Fabric
Due to the wax-resist dyeing process, batik fabric has unique qualities that require special handling when sewing. Here are some essential tips:
- Prewash the Fabric – Batik fabric often retains excess dye. To prevent color bleeding, it’s usually recommended to wash in cold water with a mild soap before sewing.
- Use Sharp Needles – Batik is tightly woven, which can make it more challenging to sew. Use a sharp microtex or universal needle (size 70/10 or 80/12) for best results.
- Choose the Right Thread – A high-quality 50 or 60 weight cotton or polyester thread works best for durability and strength.
- Mind the Fraying – The tight weave reduces fraying, but if needed, use pinking shears or a serger to finish raw edges.
- Consider the right side: The wax that creates the design sinks into the fabric, so both sides may look similar. You can look for the side with less blurring around the design.
- Combine batiks with solids: You can combine batiks with solid fabrics to give the batiks more space to shine.
- Pattern Matching – If using batik with distinct motifs, take extra care in cutting to ensure symmetrical and visually appealing pattern placement.
Caring for Batik Creations
Proper care will keep your batik projects looking vibrant and fresh for years:
- Always Wash in Cold Water – Once you’ve completed your project, make sure to always use cold water and a mild detergent to prevent fading.
- Avoid Harsh Chemicals – Bleach and strong detergents can break down the fabric’s colors and fibers.
- Hand Wash When Possible – While machine washing on a gentle cycle is acceptable, hand washing is preferred to maintain fabric integrity. Avoid twisting or wringing the fabric.
- Air Dry – Hang or lay flat to dry in the shade, as direct sunlight can cause fading.
- Storage – Store in a cool, dark place to prevent fading and damage.
- Iron with Caution – Use a low to medium heat setting and avoid steam. Use a thin cotton cloth between the iron and the fabric.
SewBatik has an excellent article on caring for your batiks, including suggestions for specific soaps and when to use and when to not use them.
Batik fabric is a joy to sew with, offering a blend of artistic expression and historical richness. While it requires some extra care, the results are well worth the effort. Whether you’re quilting, making garments, or creating home decor, batik adds a timeless and beautiful touch to any project. With proper sewing techniques and care, your batik creations can become cherished heirlooms that celebrate tradition and craftsmanship.