Smart Fitting Solutions by Kenneth D. King
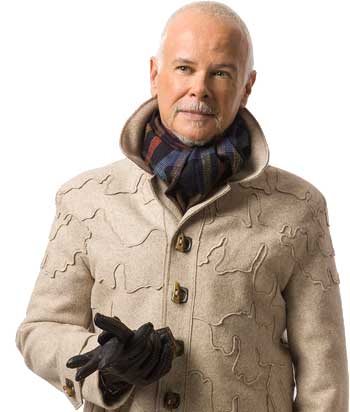
If you have ever been frustrated with trying to get a garment to fit YOUR body, don’t despair. Help is on the way! Iconic designer and sewing educator Kenneth D. King has written a new book, Smart Fitting Solutions, that demystifies the fitting process for a multitude of problem areas for women no matter what their body type.
Perhaps you have journeyed down this fitting road before and have been confused with wordy explanations and unclear instructions of what to look for and how to achieve a solution.
What you will absolutely love about this book is the clear, concise text that accompanies the hundreds of beautiful photographs that are truly worth a thousand words each. Smart Fitting Solutions is like a graphic novel for sewing. Unlike a video that whirls by quickly, the photographs provide the reader an opportunity to review the brief text, then take the time to study the picture to really see what is being conveyed.
The impressive photographs are not the only aspect that make this book unique. Scattered throughout the book are King’s personal preferences and tips. These span topics like recycling a muslin, pattern making techniques, fixing gaping necklines, and even where to begin flaring a skirt. I liked that King distinguished between conventional techniques and his own preferences, allowing the reader to understand the reasoning behind the differences.
Smart Fitting Solutions Explained
The layout of the book begins with evaluating a figure and creating a personal “croquis” or sketch from which to determine characteristics for an individual. Again through pictures, when the proportions of fashion illustrators are modified to reflect the actual proportions of the individual, it becomes quite clear why the completed garment is not as flattering as the illustrations made it appear.
Six women from the Threads staff are featured wearing several different garments that are evaluated on fit and figure flattering aspects. After “reading” each, King then gives suggestions on both fitting and style that would enhance their appearance. He even gives ideas for modifying ready to wear to salvage those non-flattering garments. His insights provide an excellent starting point for choosing the right design aspect that does not work against a particular body type.
King’s fitting approach simplifies the process into three basic categories: net loss, net gain or no net change.
While these sound like complicated accounting terms, they are just his way of saying an area of the pattern is too large, too small, or just not in the right spot.
And the remaining 80% of the book is devoted to showing us how and where to add, remove, or rotate the fabric to place it where it is needed. (In Appendix 1 he has included diagrams of a body as well as a pattern with key measurement points indicated so that the reader can easily see the points on the body and where those adjustments would be made on the corresponding pattern.)
King begins with step by step instructions for modifying a pattern based on his initial croquis evaluation to create a muslin, then “reading” that muslin to see what the drag lines and wrinkles tell us. Again, those pictures clearly illustrate the techniques he uses to make the adjustments on the muslins for each of his six subjects. Those adjustments are then transferred to the pattern.
“Once I understood the concept, I found I was reading wrinkles on everyone.” ~ Rosemary Fajgier
The more I observe, the more I understand and see how the adjustments can be applied. I am working on a top that I have made several times with stock adjustments that have never worked. I am looking forward to tweaking the fit using the methods from this book.
~ Reviewed by Rosemary Fajgier